Joints
Ductile iron pipe has a wider variety of joints available than any other piping material, giving it greater versatility and flexibility in pipeline design and installation to accommodate various applications. These joints are time proven to be strong, dependable, and bottle-tight.
Both push-on joints and mechanical joints are used with Ductile iron pipe installation. Push-on joints are comprised of a special bell with an internal groove, a plain end, and rubber gasket which is seated into the bell’s groove. This joint forms a watertight seal.
Mechanical joints most typically are used for Ductile iron pipe fittings and have four parts.
- A flange cast with the bell;
- A rubber gasket that fits into the bell recess;
- A gland, or follower ring; and
- Tee head nuts and bolts for tightening
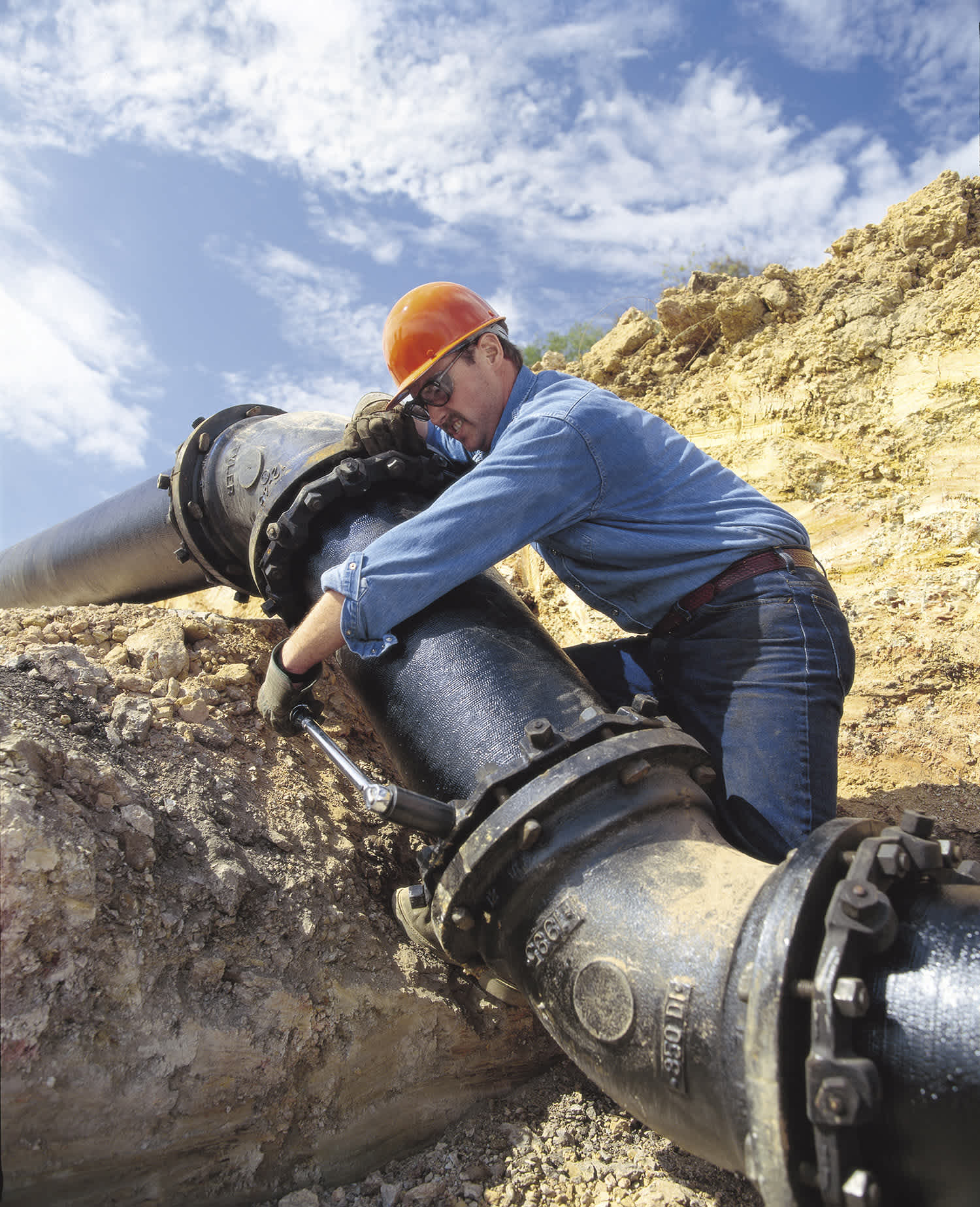
Choose the Correct Gaskets and Joints
Ductile iron pipe offers wide availability for all manner of applications, from the standard push-on joint and SBR gasket, to the many available restrained joints and gaskets that address contaminated soils and elevated temperatures. Ductile iron pipe with boltless ball and socket joints is an extremely versatile product for use in subaqueous construction.
Gaskets
The five most common gasket types used with Ductile iron pipe each have maximum service temperatures and specific uses. Most gaskets used for typical water pipe projects are made of synthetic rubber. The Styrene Butadiene (SBR) rubber gasket is most commonly used in conjunction with mechanical or push-on joints for water lines that have normal service temperatures (120º to 150ºF). Condition-specific gaskets are available for pipelines that call for special service requirements or are installed in areas susceptible to hydrocarbon contamination.